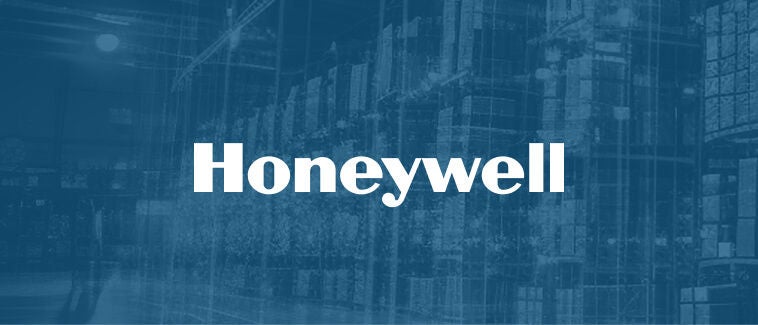
CUSTOMER STORIES
SK AeroSafety Soars with Data-Driven Aviation Maintenance Solutions
SK AeroSafety leverages Snowflake and Maxa to gain insights into global operations, streamline component maintenance, and support predictive maintenance for safer, more efficient aircraft.

Industry
ManufacturingLocation
Wokingham, United KingdomStory Highlights
- Streamlined visibility for better service: Using Snowflake and Maxa, SK AeroSafety can view real-time data across global sites, helping them deliver quality service faster to keep planes safely operational.
- Comprehensive dashboards to track trends: Maxa’s dashboards built on Snowflake allow SK AeroSafety to track technician hours, shop capacity and revenue trends, leading to data-driven improvements in efficiency and margins.
- AI/ML-powered predictive maintenance: Using Snowflake and its AI and machine learning capabilities, SK AeroSafety delivers a predictive maintenance solution that helps predict the work coming into the shop. SK AeroSafety hopes to create a solution that would help anticipate potential issues in aviation components before inspection, enhancing reliability and turnaround speed.
Video Transcript
This transcript was automatically generated
Ben te Beek. I'm the CEO of the SK Aero Safety Group. The way the aviation component maintenance works is we inspect the component. Our technicians write down what's wrong with the component. They put it back into a serviceable condition, and then the product is shipped back to the customer to eventually be put on an aircraft. And what's most important in that process for the customer is how quickly we can perform that service for them.
Monica Badra. I am the founder of Aero Next Gen, which is a digital solution brokerage in aerospace. We have customers that are running component repair facilities and don't have any visibility into the performance of their shelf floor.
We use a product that Maxa developed, which is a native app that sits on top of Snowflake.
So I don't actually see the Snowflake product, directly. I just see what the end user sees in in in this instance, which is the data analytics that Maxa have built on top of it for us.
Maxa being built on Snowflake is really important because it allows us to aggregate large datasets without causing any latency on the actual enterprise solutions. We were able to deliver is dashboards that allows them to see what is the current inflow, outflow of the shop so they could start measuring a trend of capacity.
We built utilization dashboards so they could see how many hours the technicians are being paid versus what they're clocking. And now with Snowflake, creating a collaborative data environment, we wanna be able to build native applications that any single aviation party can plug and play into these solutions. The predictive maintenance solution that we've delivered is basically like a sales and operations planning module. We built one piece, which is the sales model, which uses artificial intelligence and machine learning to predict the volume of work coming into the shop. It's a full three sixty benefit for the operations as well as to our customers.
Maxa and Snowflake helped streamline that process, basically taking the data from our system, and within a few weeks, introduce an analytics model that we could use that gave us insights into all of the revenue and margin data that we have across our group. We can now see the information at an aggregated level, across all our businesses, across everywhere in the world. That has resulted in a in a, what we hope to be this year, a one to two percent uptick in our margins. We can now see the analysis instantly, very quickly, and we can use it to make better decisions. Making sure that the airline gets the components that are maintained back as soon as possible ensures that they can keep planes flying safely. What SK hopes to do with AI and MLs through the use of Maxa and Snowflake is one to work on predictive maintenance, where we can actually predict what is wrong with the components that come into our shop even before we physically looked at it.